Finishing by Gardette
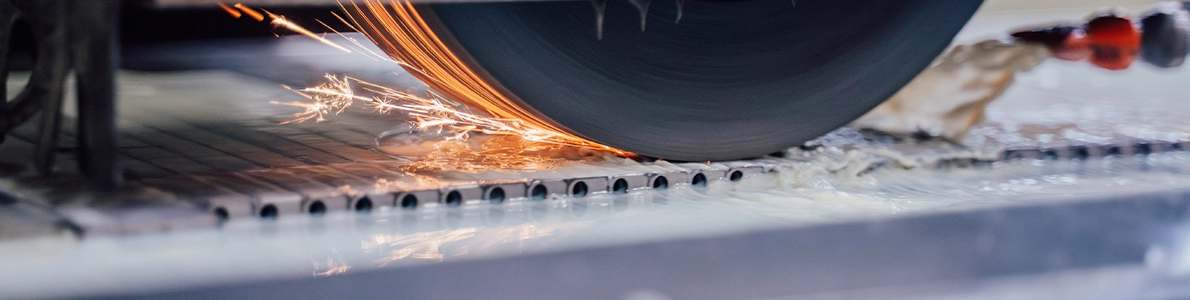
Finishing: the final touch that makes a world of difference
Making keys or made-to-order parts is not just about the initial manufacturing phase. Various finishing processes are essential in completing the overall production process. Mechanical parts undergo such techniques and treatments in order to obtain the characteristics required for their final use. In this article we are going to look at the different types of finish offered by Gardette.
Stay with us to find out more!
- What are finishing processes?
- Finishing at Gardette Industries
- Treatments
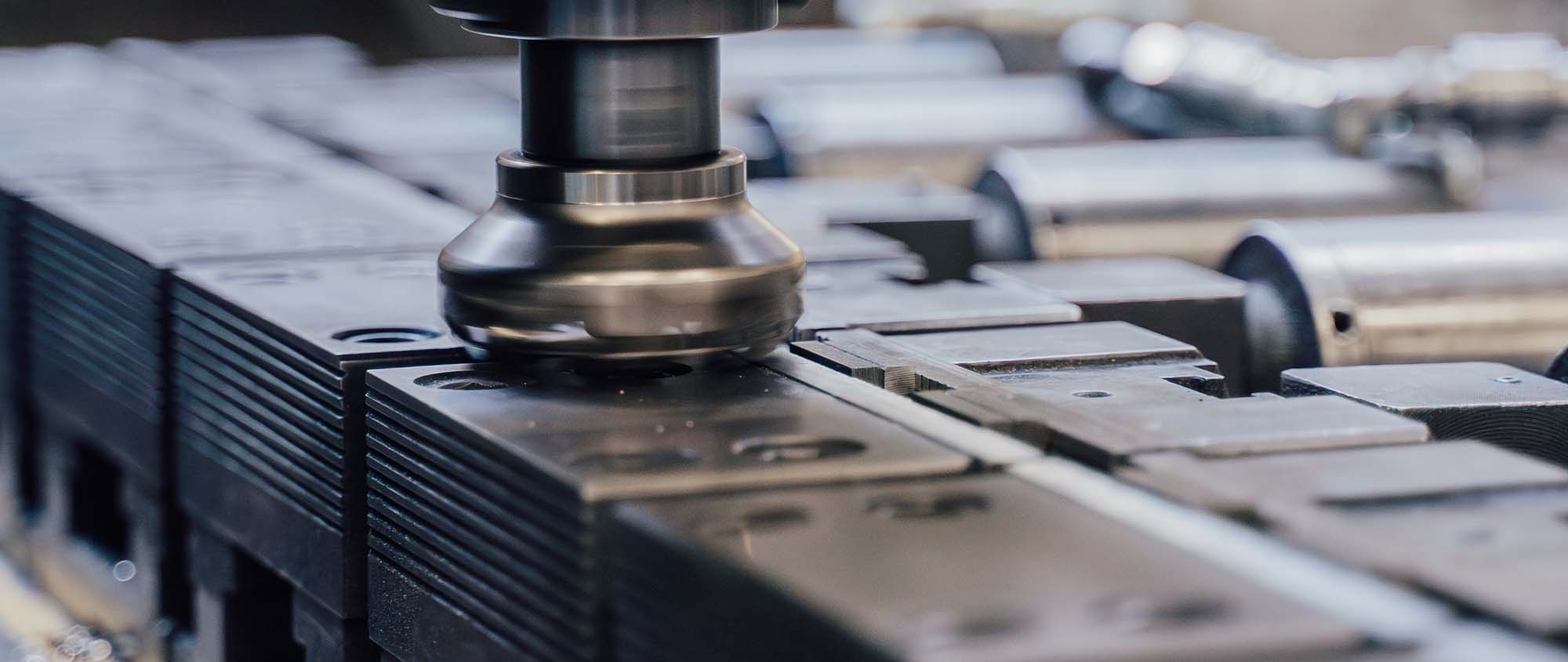
What are finishing processes?
Finishing is a crucial step in the process of manufacturing a mechanical part. It involves carrying out some final machining operations to give the part its final shape and dimensions, either to make it functional or to move on to the next production stage.
Finishing operations also enable us to tweak parts' tolerances and surface finish using techniques such as chamfering or drilling. Here at Gardette, we have a fleet of cutting-edge machine tools which we use for high-precision, efficient finishing processes.
Finishing at Gardette Industries
At Gardette, finishing involves mechanical work that aims to give the part its final shape.
To do this, we use various specialist machines.
Cutting and stock squaring operations
- Milling machines for various operations: Milling machines are used for cutting parts, stock squaring, as well as creating shoulders, chamfers and gradients on the parts.
- Cutting & stock squaring: Cutting the parts according to the desired dimensions; while stock squaring allows us to create flat surfaces on the parts in order to achieve precise tolerances regarding the perpendicularity between the different sides.
Working on parts using machining centres
Machining centres are automated machine tools that can carry out various operations such as drilling, tapping, milling and chamfering with high precision:
- Drilling & tapping: creating precise holes and threads in parts.
- Milling: removing material to create flat surfaces or specific shapes.
- Chamfering: creating bevelled edges on parts.
Use of grinding machines
How grinding machines work: Grinding machines with abrasive wheels are used to polish and even out the surfaces of the parts, for precise tolerances and a high-quality finish.
Types of grinding machines at Gardette
- Surface grinding machines: used for grinding a single flat surface on a part.
- Double disc grinding machines: used for grinding two opposite surfaces of a part at the same time, allowing for perfect flatness.
Customising parts and automation
- Marking parts: We carry out marking operations on your parts with a dot peen marking machine, allowing you to easily (and permanently) customise parts.
- Automation of the production process: We have two robotic systems used for loading and unloading the machining centres, thus optimising production efficiency.
Treatments at Gardette Industries
Heat and surface treatments are used to achieve the desired structure, aesthetic or protective aspect for a mechanical part.
Here at Gardette, we have an oven that allows us to perform annealing heat treatment.
As well as this, we offer various types of heat and surface treatments depending on each client's specific requirements. No matter the process - be it quenching, tempering, zinc coating / galvanising, burnishing, painting, etc. - we have trusted partners with whom we work regularly to offer our customers a comprehensive service and meet specific requirements.
In short, finishing is an essential stage when manufacturing parts, involving certain mechanical operations and treatments. At Gardette Industries, we use technologically advanced machine tools to guarantee an accurate and effective finish, whatever your particular requirements may be.
We promise to provide an answer to your enquiry within seven days.
Talk to us