Key responsive manufacturing®
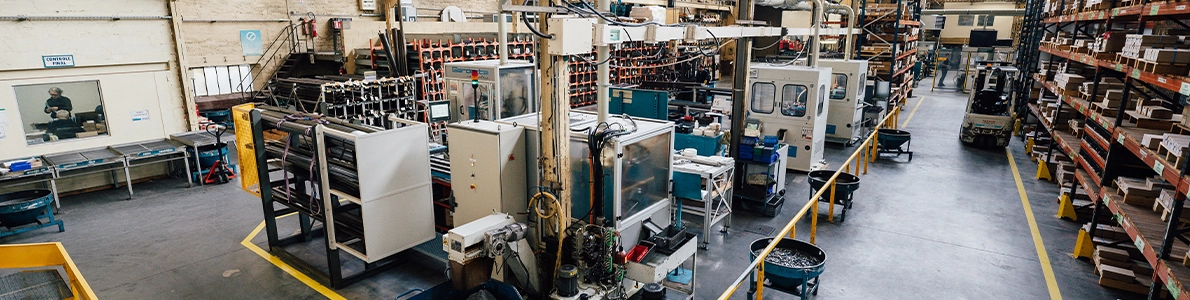
Key responsive manufacturing: our philosophy
Key responsive manufacturing®: our dedication to ultra-responsive and high-end industrial service à la française
For several years now, we have been using the responsive manufacturing method: a pragmatic combination of lean manufacturing & Agile methods for industrial management with short lead times, with the necessary technology for company processes, in order to better serve both production and the customer.
Some key aspects of our company philosophy:
- The world and its dynamics are changing, forcing companies to act and respond quickly
- Gardette's "key responsive manufacturing" values
- The seven major pillars of Gardette's key responsive manufacturing approach
- The world and its dynamics are evolving, so are we
- Values of GARDETTE key responsive manufacturing
- The main principles of GARDETTE key responsive manufacturing
The world is evolving - so are we
In the world of industry, companies are constantly challenged with meeting customer expectations while also ensuring just-in-time production and improving return on investment. In an ever-globalised world, and following several crises, these challenges have been exacerbated. Manufacturers must now serve various markets, dealing with complex supply networks that have replaced traditional linear supply chains.
This was accentuated by the COVID-19 pandemic and the crisis in Ukraine, for two major reasons:
- Many countries temporarily closed production and, in some cases, their borders. These travel restrictions disrupted supply chains and created shortages (of materials, energy, finished products, etc.) across the board. As a result, procurement practices were completely changed, with companies forced to diversify their suppliers, often opting for geographically closer suppliers to reduce dependence on transport.
- Working from home, which was previously only the norm in the service sector, has also become widespread in industry, bringing other related practices with it, such as the increased use of information and communication technologies (ICTs) to facilitate remote work and collaboration, e-commerce as well as the use of data feedback.
At Gardette Industries, these developments compelled us to adapt. To deal with them, we came up with an extremely agile industrial management strategy that is not only applicable to production but to all other company processes as well: key responsive manufacturing.
Key responsive manufacturing, our new leitmotif, allows us to face up to all these challenges and become even more competitive in an ever-globalised industry - not just as a manufacturer, but also as a provider of solutions for our clients through pragmatic management right from the quotation request.
Values of Gardette key responsive manufacturing
With key responsive manufacturing, our companies follow very different production models: predictive, agile, lean, etc.
The product's entire life cycle, from the innovation stage to delivery, is streamlined in order to produce only what is needed (and quickly!), meet quality expectations, and eliminate any additional costs, while still being able to grow and adapt to changes in demand.
Allowing customers full insight into all production stages is critical to the success of this approach. As historic industrial manufacturers, we needed to break down walls between our different departments and ensure optimal integration of all systems and processes involved in the chain. Other key aspects of responsive manufacturing include continuously collecting data in real time at each stage of business (from opportunity research to after-sales), forecasting and detecting any changes, as well as manufacturing to order.
In key responsive manufacturing, production begins when it is “necessary” and optimal.
This approach has allowed us as a manufacturer to develop a varied, complex product portfolio while drastically reducing additional production costs and eliminating ghost expenses.
Finally, constant influx and analysis of production and organisational data ensures that products meet our customers' quality and compliance standards, as well as those of regulators issuing product certifications and accreditations.
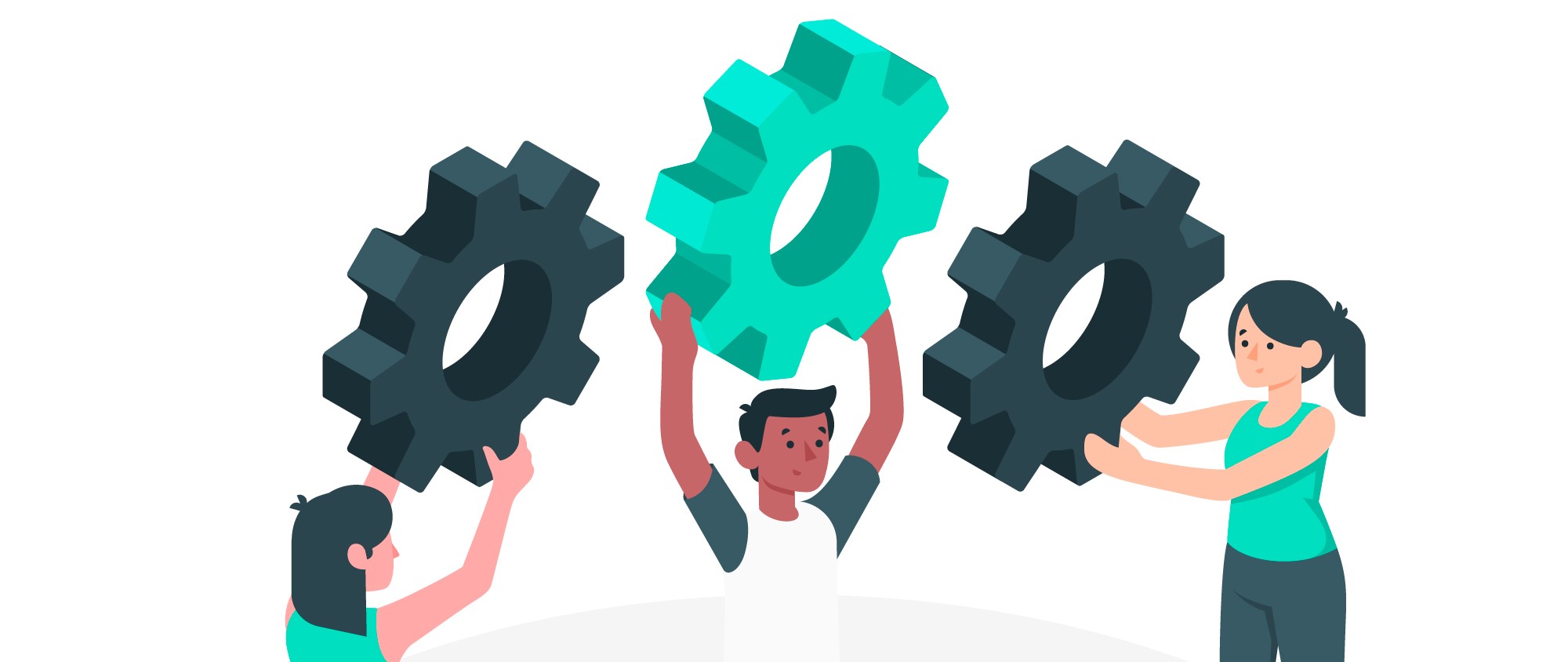
Main principles of our key responsive manufacturing approach
Agile management, even at the top
Our board of management and executive committees meet at least once a week for a quick qualitative and quantitative KPI review.
This approach is directly linked to our strategic plan, which is adjusted at least every year, and takes into account modelled forecasts of our clients' needs, both recurrent and sporadic.
Key point: the KPIs we measure and monitor can also be adapted according to challenges and weekly developments in the status and variety of current offers and orders.
This management method promotes two things:
- Pragmatic adaptation of a “common thread” plan rather than incorrect theory-based application: In an ever-evolving industrial setting, it is paramount to adopt an ultra-flexible strategy that can be tweaked to meet new challenges and goals. Agile management allows us to work on short-term goals while maintaining a long-term strategic vision. This helps our business to quickly adapt to changes in the market and make informed decisions.
- Management that looks at live operational indicators rather than previous results: Agile management is based on a goal-oriented approach, focusing on real-time operational indicators rather than past results. This approach allows management to quickly adapt to changes and challenges in the market, making informed decisions based on reliable and up-to-date data. It also helps identify potential problems earlier on, so that corrective measures can be implemented to improve results.
A tailor-made sales solution
We have adapted our sales department to “new” and diverse market requirements - a mix of small & medium quantities (80% of orders) and large quantities (20% of orders).
Different customers, different (and new) markets, different individual needs (quality/quantity, etc.)
From lawn mower repairers to car manufacturers, customers in the post-Covid era want increasingly responsiveness service.
However, traditional industrial systems aren't suited to modern customers' expectations.
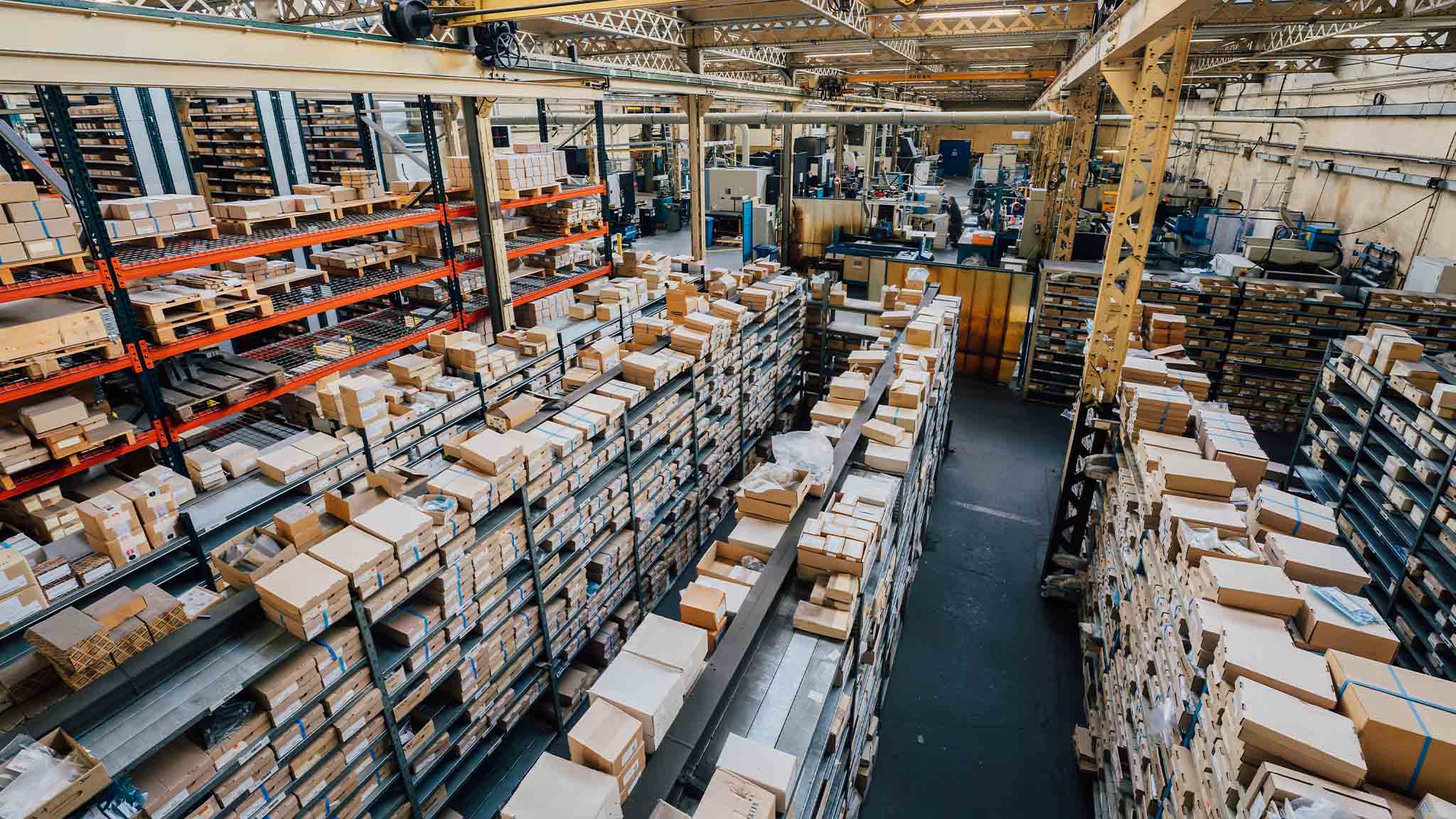
Choosing a strategy: make everything or buy from local expert partners?
In collaboration with our quality department, we have developed partnerships with a solid network of accredited suppliers, allowing us to offer various solutions to our customers.
As a manufacturer, we have focused on the backbone of our differentiating processes by concentrating investment innovation on “in-house” processes.
Nonetheless, when we don't have the necessary machine or process at our disposal, we may offer to have part of the production done by one of our accredited partners, rather than taking the risk of being too expensive or having too long a deadline. This allows us to meet customer demand while also ensuring the level of quality you know from Gardette. Benefits of this strategy include:
- Reduced deadlines: By having access to a network of local partners, we reduce production times with the help of their know-how and production capacities. This enables us to respond more quickly to customer requests and to increase responsiveness.
- Diversification of skills: Our partner suppliers have skills and production equipment that complement those of our company. This allows us to expand the range of finishes and types of products we offer to customers and sometimes even to improve the quality of the products we manufacture.
- Cost optimisation: By having (a portion of) customer requests manufactured by accredited suppliers, we can optimise production costs by exploiting the competitive advantages of these suppliers. This reduces the time to cost ratio for our company and, subsequently, for our customers.
- Quality guarantee: We invest to ensure that our partners have the skills and capacities needed to provide quality services via a complete die, revisited to the highest standards by our quality department. This allows us to guarantee high-quality services to customers and increase their satisfaction.
Our hyperflexible "production islands"
Cellular production, or island production as we like to call it, involves grouping various stages of production together into a compact cell or island dedicated to a specific product or group of products with similar characteristics. Unlike assembly line production, where each product goes through each production stage in a set order, cellular production allows us to work on several products at the same time, all while offering greater flexibility in the order in which the production steps are carried out. This type of production is possible thanks to carefully measured investment, allowing us to constantly pivot between push and pull without losing the most important thing in our job as producers: productivity.
Cellular production offers us:
- Flexibility: The cell / island approach allows greater flexibility when producing different types of products. Islands can be designed to meet certain specific requirements, such as manufacturing custom products or small series.
- Versatility: The workers on each cell are extremely autonomous and constantly trained on the latest equipment and processes. This allows for a certain level of adaptability even at peak production as well as a better HR approach.
- R&D innovation in processes & automation: Our performance is measured by our ability to have “the right machine for the right process at the right time”, as well as having the right products. The whole logic for measuring our performance has been redesigned to suit humans rather than machines.
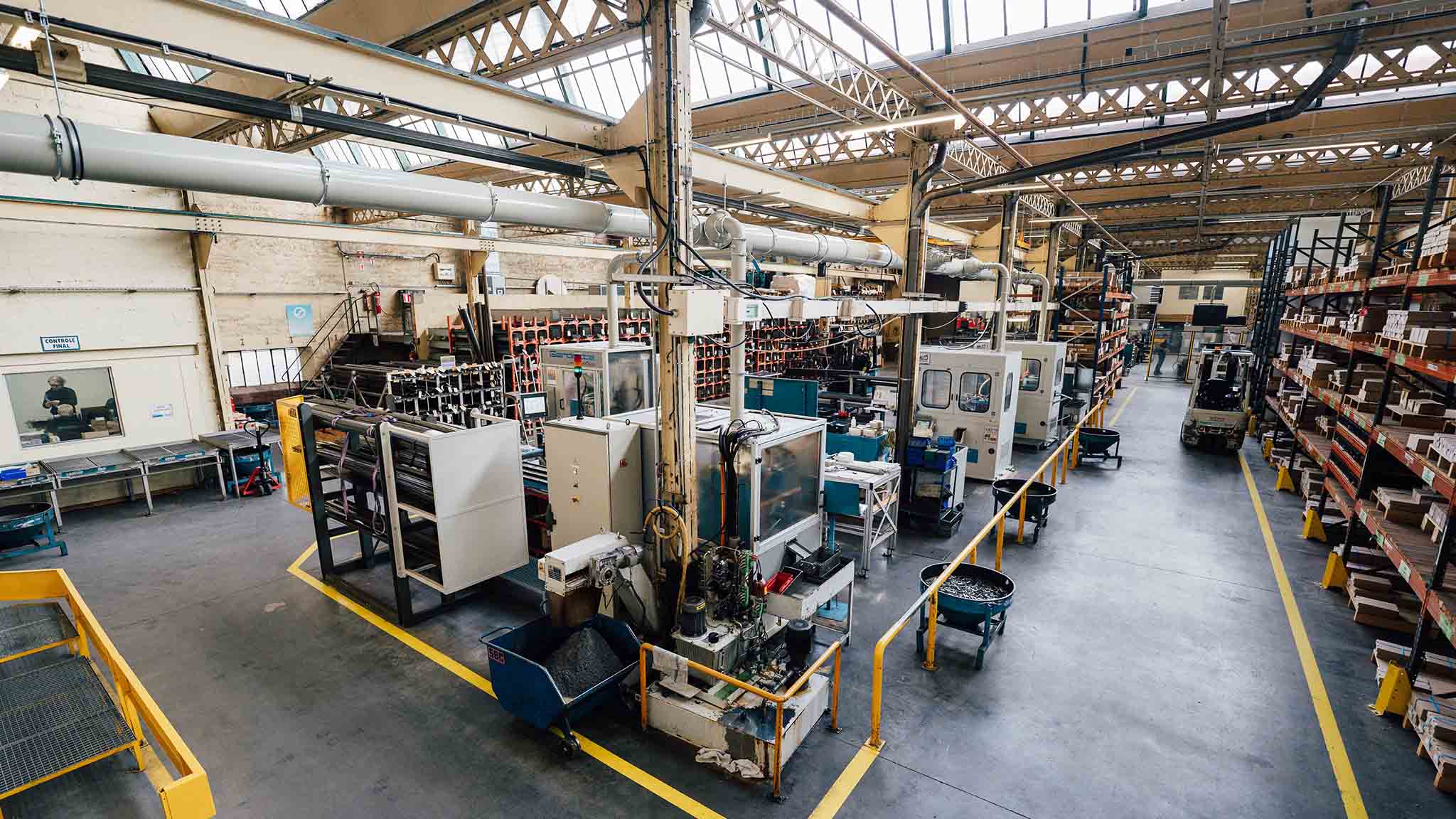
Valuing women and men where they are needed
Everything that can be automated should be automated, but automation does not mean everything is done by robots. Of course, our robots can load and unload machines and much more, but humans have a central role to play in our company. While repetitive tasks can often be carried out by increasingly efficient and precise machines, human input remains essential here at Gardette.
- Increased quality: Cellular production enables us to better control different stages of production, as employees share responsibility for a specific set of tasks. We have noticed that this reduces errors and improves overall quality.
A fully internal value chain
At Gardette, we quickly noticed the advantages offered by controlling the entire value chain, from start to finish, within our SME. Right from the start of production (at the raw material stage), we can adapt each stage to clients' individual needs, quickly identify new market trends and react to them, improving our company's overall responsiveness.
- Vertical integration of production of our own raw material, cold worked at our factory in Villars, France. This somewhat crazy bet was taken in 2013 with the aim of industrialising our company, which at the time was almost artisanal, albeit with unique know-how. Today, this decision is the cornerstone of what became a major asset in the wake of Covid and amid an unstable global market. In just a few days, we now manufacture amounts that used to take us several months.
- Reduced lead times: By controlling the whole value chain, we reduce production times by eliminating delays and waiting times between the various stages of production. This allows for faster production and quicker delivery of products to our customers.
- Continuous automated quality control: By controlling the entire value chain, we can control each stage of production and quickly detect quality problems. This reduces the risk of quality defects and improves customer satisfaction.
- Flexibility: Controlling the value chain allows our company to be more flexible in the production and delivery of products. This means that we can quickly adjust production according to customers' needs or market trends, improving our overall responsiveness.
- Continuous improvement: By handling all reported data in real time, we can set up continuous improvement processes in order to constantly improve quality, productivity and responsiveness.
- Cost control: Full control of the value chain means we can better control production costs, identifying sources of unnecessary costs or inefficiencies in our production processes. This makes our company more profitable while maintaining high-quality products.
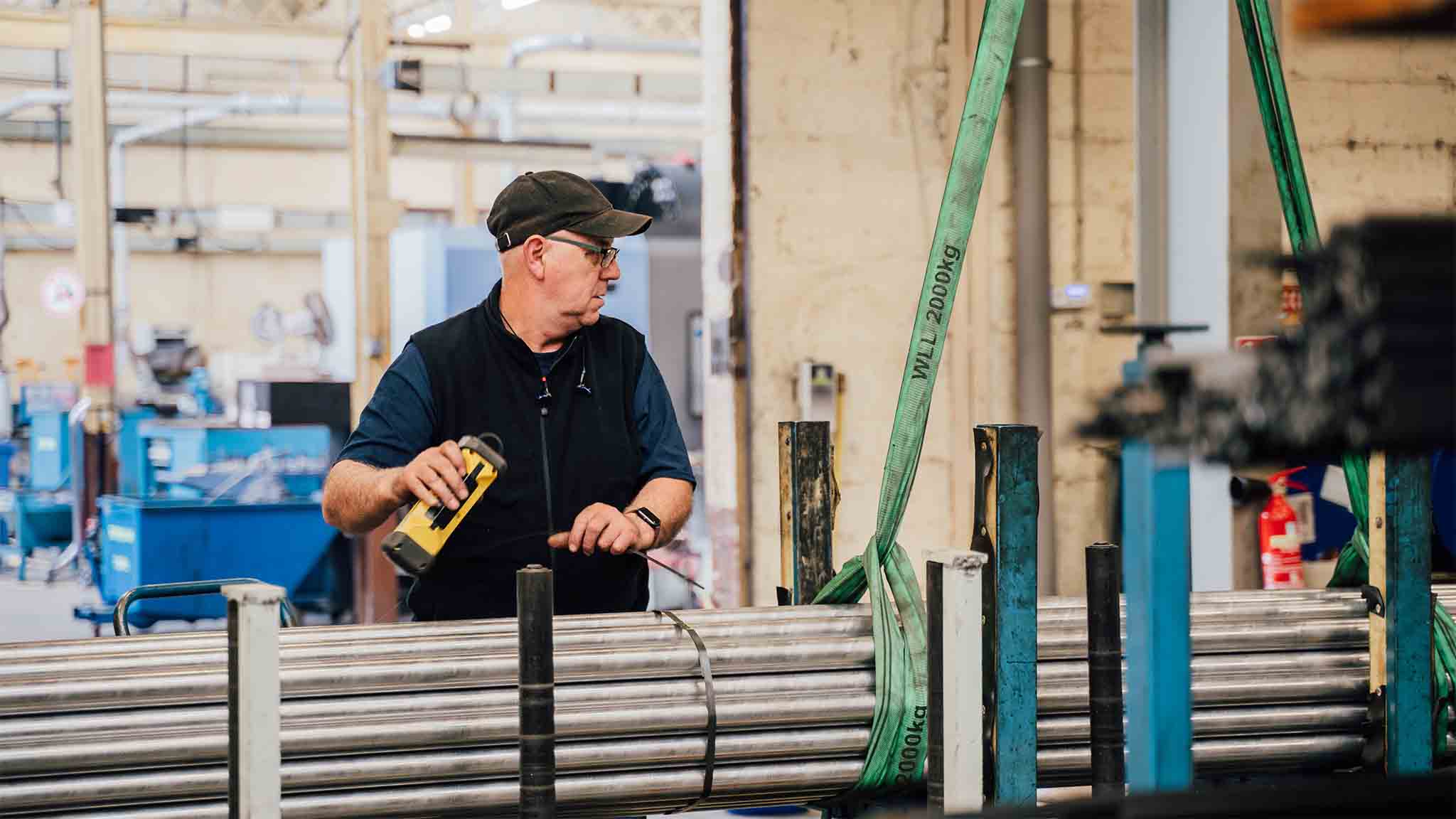
Digitalisation
In recent years, we have invested heavily in both internal and external digitalisation. The roof of this was one simple observation: the market is changing and so are consumers. Buyers today don't have the same habits as buyers from ten years ago, making it paramount to provide effective and easy-to-use digital tools. The main elements of our digitalisation process include:
- Implementation of a digital marketing strategy: By using online communication channels, our company can better target its potential customers and personalise offers. This enables us to quickly respond to customers' enquiries and better understand their needs, in turn improving the quality of our products and services.
- Implementation of a modern CRM system linked to our marketing data: An effective CRM system makes it possible for us to centralise customer information in a database that is accessible by all the company's departments. This improves communication between different departments, in order to better understand customer needs and quickly offer solutions. The customer experience is also enhanced through adequate follow-up.
We promise to provide an answer to your enquiry within seven days.
Talk to us