How keys are manufactured
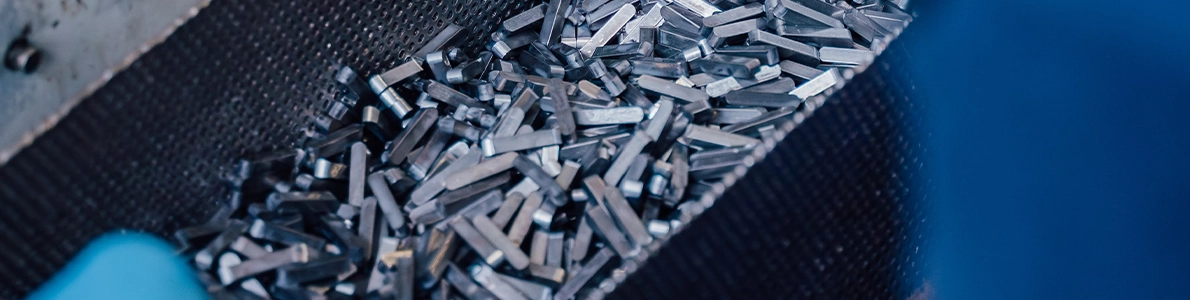
How are keys made?
Keys are a mechanical transmission component that allow for the rotation of a shaft & hub assembly. How keys are manufactured can vary depending on the type of key required, but the process always involves several manufacturing stages, from design to finishing. In this article, we will explain the main stages that go into making keys.
- Cold drawing, rolling & shot blasting
- Cutting
- Finishing
- Vibratory finishing
- Treatments
- Quality
- Logistics & packaging
- Delivery
Drawing, rolling and shot blasting
The first stage in manufacturing a standard key is shot blasting, rolling and cold drawing the raw material to give it the key's final diameter. This step reduces the raw material to the desired size for the key. Here at Gardette, we have invested heavily in know-how and equipment surrounding cold steel processing. This equipment enables us to produce a wide variety of standard and special steel profiles.
Cutting
Once the raw material has been prepared, the key is cut using tools such as saws and milling cutters. This is when the key is given the desired length and shape. At Gardette, we have both circular and band saw milling machines. We also have form milling cutting machines, allowing us to make form A keys and form C keys with record productivity.
Finishing processes
The next stage in manufacturing a key is finishing. This can be drilling or tapping a hole via milling; making simple chamfers with a belt sander; or making a gradient using numerical control. This stage is where grooves, countersinks and other shapes are created so that the key remains in position during use. At Gardette, we are equipped with flat surface grinders and double disc grinding machines, 3 and 4-axis machining centres, traditional milling machines and two robotic systems used for loading/unloading parts.
Vibratory finishing
Tribology is the study of friction, wear, and lubrication. Vibratory finishing makes it possible to apply the principles of tribology by wearing down parts via a mixture of abrasives and passivation liquid. Despite its often-negative connotations, this wearing down is necessary in order to ensure that are parts are compliant with customers' requirements. It allows us to remove burrs created in previous manufacturing processes, to improve the parts' surface roughness and to slightly curve / radiate sharp edges, making our keys easier to use and assemble. At Gardette, we have two technologies at our disposal to carry out this essential step: vibration, which involves mixing the parts with the abrasives in a vibrating bowl at a predefined frequency and amplitude, as well as centrifugation, whereby the parts are spun by a rotating bottom. Although centrifugation is the most efficient process, parts can make for certain geometrical limits (deformations, sizes of the parts, inertia caused by mass, etc.).
Treatments
Keys can undergo various types of treatments to enhance their mechanical properties and resistance to corrosion and wear. There are two types of treatments: heat treatments and surface treatments. Heat treatments make it possible to modify the mechanical properties of parts by modifying the microstructure. For example, quenching + tempering can improve a part's mechanical strength and hardness thanks to the formation of martensite, while still maintaining a certain maximum elongation (depending on the duration and temperature of annealing).
Surface treatments form a protective layer on the steel in order to protect it from its environment (for example, zinc plating can be used to form a sacrificial anode on parts for a certain period of time, i.e. the zinc will oxidise instead of the iron contained in the steel in order to protect the part, by first forming white rust (which comes from the zinc) and then red rust (from the iron).
Quality
From the stockroom to shipping, we carry out systematic checks on our raw materials, semi-finished and finished products. When a batch of raw material is received, we verify the steel manufacturer's certificate and the dimensions of the batch before the material is validated and recorded in the ERP system. During manufacturing, parts are checked via cross-sampling by the operator, the sector manager as well as our quality department. Before being stored or being made available for shipment, all production orders are subject to a final check by the quality department.
During this final quality control stage, any documents that the customer may require are issued (certificate type 2.1, 2.2, 3.1 as per NF EN 10204, measurements, treatment certificates, FAI). We can also set up checkpoints, monitoring production capacity and measurement resources as well as control plans in order to produce prototype files and full initial samples (DVI and PPAP level 3).
Logistics and packaging
Once the key has been manufactured and quality checked, it is ready for storage and/or shipping. The keys are then packaged in appropriate materials (bags, cardboard, pallets, etc.) to protect, store and transport them safely throughout the supply chain. The packaging process plays a crucial role in protecting keys during storage and transport. At Gardette, our packaging respects official standards and regulations. We can also adapt to clients' specific requirements (bags, cardboard, customer-specific packaging, etc.).
The logistics stage essentially means planning delivery according to the needs and deadlines agreed with the client. At Gardette, logistics includes several different activities - inventory management, following up on orders during production, keeping customers informed, shipping management and returns. This process is aligned with business goals and takes budgetary and operational constraints into account. Well-planned logistics improves operational effectiveness, minimises risks and increases customer satisfaction.
Delivery
The final step in manufacturing a key is delivery. The key is shipped to the customer according to the previously agreed terms and timeframe. At Gardette, once the order has been prepared, it is loaded onto trucks (depending on the nature of the goods, the weight and/or the requirements of the order.)
Delivery is a key stage in the overall process. An efficient and well-managed delivery can have a positive impact on customer satisfaction, company image and business relationships.
We promise to provide an answer to your enquiry within seven days.
Talk to us