Key manufacturer for 100 years
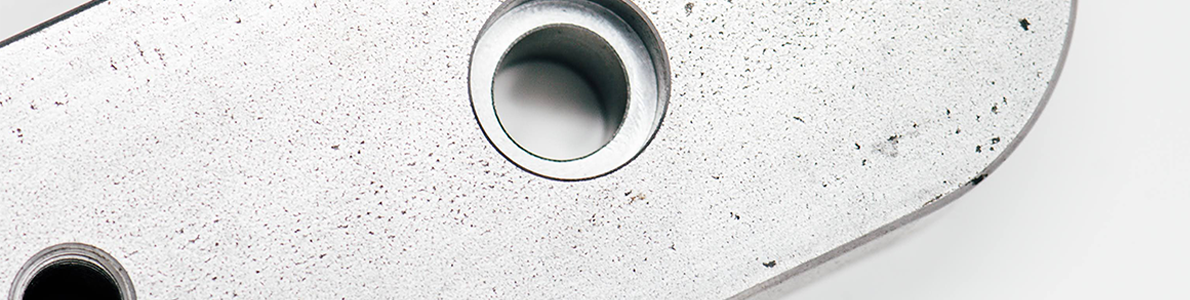
The characteristics of a key
In this article, we are going to show you what a Key, how it is made, its current applications, and the benefits it offers. Whether you are an engineer, technician or simply curious to discover how these small parts work, you have come to the right place! Let us guide you through the fascinating world of keyways.
- What is a key?
- How do you make a key?
- The applications of the key
- The advantages of the key
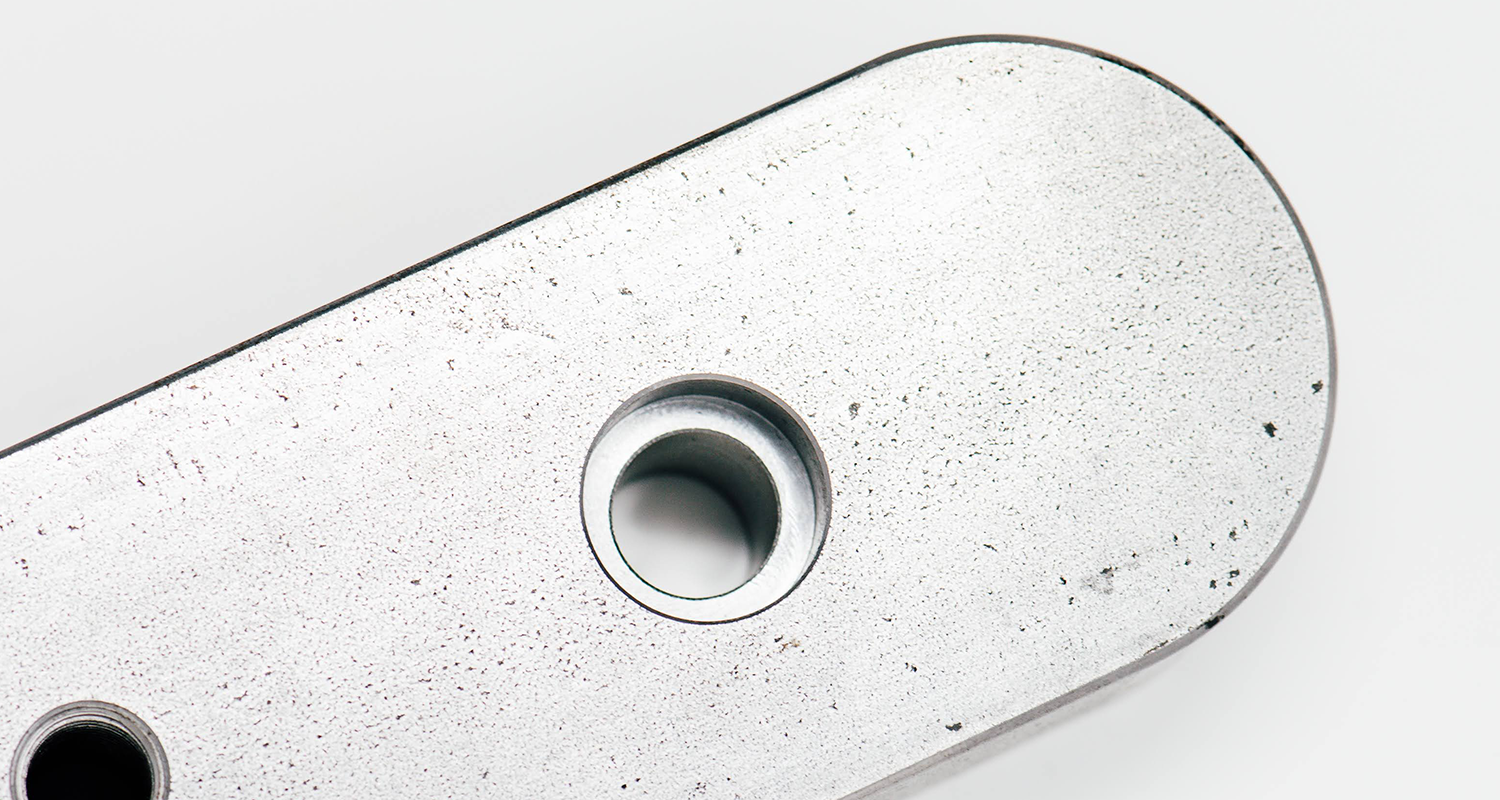
What is the role of the key?
The key is an essential mechanical part for the transmission of motion in many industrial applications. It is used to rotate two parts, such as a shaft and a pulley or a gear, in order to allow the transmission of force and movement. Different types of keys exist, such as Keys round toe (shape A), straight toe (shape B), with a round toe and a straight toe (shape C), as well as heel keys and disc keys.
The manufacture of the key
The manufacturing process of Keys may vary according to the needs and specifications of each application.
Most keys are made from resistant materials such as carbon or stainless steels, but also non-ferrous ones such as brass, bronze...
The material grade and their dimensions depend on the requirements of the application, in particular the size of the shaft and the pulley as well as the forces to be transmitted and the environment in which it will be subjected.
At Gardette Industrie, we manufacture our keys with materials such as medium-hard steels, treatment steels, stainless steels, Exotic materials (High-alloy steels, complex stainless steels, Hastelloy/Monel/Inconel nickel alloys...) or any other material appropriate to meet the customer's needs.
The first step in the manufacture of Keys therefore consists in the choice of the material which will depend on the specific application and the requirements of the customer.
At Gardette, we are the only manufacturer in the world to have our own cold rolling, drawing and heat treatment plant. This equipment allows us to manufacture a wide variety of standard and special profiles in various materials such as steel, stainless steel, aluminum and copper and nickel alloys...
Once the material is selected, we cut it to the desired length and Keys are machined using special machines equipped with cutting tools such as saws or milling machines. At Gardette, this step is carried out in our Debit sector. Form B keys (straight ends) are manufactured using cutting or sawing machines. For the Keys Shape A and all the keys having complex shapes at the end, the two rounded ends and the length are obtained by a machining operation with special shaped tools, thanks to unique technologies that we have developed specifically.
At Gardette, we offer a wide range of finishing operations, adapted to the specific requirements and needs of our customers. Our machine park includes numerical control machining centers, robotic cells, as well as a grinding workshop (flat and double-sided) to guarantee ultra-precise tolerances or roughnesses imposed in the specifications. In addition, we have a long calibration island that allows us to perform operations such as material cubing, creating shoulders or slopes on the parts.
Finally, we are also integrated with a fleet of ultra-modern vibratory finishing machines to meet various deburring finishing needs and ensure the optimal quality of our products.
Vibratory finishing is an important step in the manufacturing process to improve the quality and finish of parts. It removes burrs, improves the surface condition of parts, and radiates sharp edges, which can improve their appearance and functionality. At Gardette, there are two technologies used for vibratory finishing: vibration with vibrating bowls and centrifugation with rotating bottoms. The choice between vibration with vibrating bowls and centrifugation with rotating bottoms depends on the specificities of the parts to be treated, the desired finishing results and the requirements of the manufacturing process.
Once the Key manufactured, it may be subjected to a surface or thermal treatment to improve its appearance, its resistance to corrosion and wear.
At Gardette, we offer a complete range of surface and thermal treatments to meet the specific requirements of our customers. The most common surface treatments are zinc plating, burnishing, phosphating, and painting. As far as heat treatments are concerned, we carry out tempering, tempering and annealing. We understand that each customer has specific heat and surface treatment needs based on their applications and requirements. We are committed to providing tailor-made solutions to meet these needs, using cutting-edge techniques and ensuring optimal treatment quality to ensure the satisfaction of our customers.
The final step in our process at Gardette is to perform a thorough check of the key. During production and once the manufacturing operations have been completed, we carry out a meticulous check to ensure that the Key meets the most stringent quality standards. Our qualified technicians use state-of-the-art, high-precision measurement tools to verify dimensions, tolerances, and other critical specifications to ensure that every key that leaves our workshop meets customer requirements. Quality is a priority at Gardette and we are committed to providing high quality parts to our customers.
The applications of the key
Les Keys are commonly used to transmit the power of rotation from a shaft to a rotating part, such as a pulley, a gear, or a gear wheel. They are used in various industrial machines, such as motors, machine tools, manufacturing equipment... Keys can also be used in specific applications, such as power transmission systems for conveyors, lifting equipment, transport equipment, transport equipment, agricultural machinery, etc. At Gardette, we collaborate with the sectors of the automotive, civil and military aeronautics, textile, nuclear, industrial, transport equipment, transport equipment, agricultural machinery, etc. At Gardette, we collaborate with the sectors of the automotive, civil and military aeronautics, textile, nuclear, mold, and pump manufacturers....
The advantages of the key
La Key has numerous advantages compared to other mechanical fixing means such as cable ties or welding. Here are a few benefits:
- High torque transmission: Keys are designed to transmit high torques in mechanical assemblies. For example, a 25 mm wide key can transmit a torque of over 700 Nm, making it a robust option for applications that require high torque transmission.
- Stiffness and stability: The Keys offer a rigid and stable connection between the assembled elements, which can be important in applications requiring high precision and dimensional stability.
- Durability: Keys are typically made of steel or stainless steel, making them resistant to corrosion, wear, and other types of damage, which can contribute to extended assembly life.
- Ease of installation: The Keys are relatively easy to install and replace in an assembly, with simple and well-established assembly procedures.
- Wide availability: Keys are widely used and available in numerous sizes, shapes, and configurations, making them a common and easily accessible option on the market.
- Standardized design: The keys are manufactured according to standardized design and manufacturing standards, making it easy to integrate them into existing assemblies or into new designs.
In conclusion, the Keys are essential elements in mechanical systems to ensure efficient and secure power transmission. Appropriate use, regular monitoring, and adequate maintenance are required to ensure their proper functioning and to prevent potential failures.
We are committed to providing an answer to your problem in less than 7 days.
Get in touch